亮点评述
多级混流式混输泵气液两相增压特性
多级混流式混输泵气液两相增压特性
戴晓宇 徐强
杨晨宇苏筱斌郭烈锦
(西安交通大学动力工程多相流国家重点实验室,陕西 西安 710049)
DOI:10.11949/0438-1157.20240924
引用本文: 戴晓宇, 徐强, 杨晨宇, 苏筱斌, 郭烈锦. 多级混流式混输泵气液两相增压特性[J]. 化工学报, 2025, 76(2): 554-563 (DAI Xiaoyu, XU Qiang, YANG Chenyu, SU Xiaobin, GUO Liejin. Gas-liquid two-phase pressurization characteristics of multistage mixed-flow multiphase pump[J]. CIESC Journal, 2025, 76(2): 554-563)
引 言
1 实验系统
1.1 实验环路
1—储液罐;2—给水泵;3—流量调节阀;4—液相流量计;5—静态混匀器;6—三级混流式混输泵;7—扭矩转速仪;8—变频电机;9—出口控制阀;10—高压截止阀;11—气相调节阀;12—空气压缩机;13—高压储气瓶;14—气液分离器
1—liquid tank; 2—centrifugal pump; 3—flow regulating valve; 4—liquid flowmeter; 5—mixer; 6—three-stage mixed-flow pump; 7—torque tachometer; 8—variable frequency motor; 9—outlet control valve; 10—high-pressure globe valve; 11—gas-phase regulating valve; 12—air compressor; 13—high-pressure gas storage cylinders; 14—gas-liquid separator
表1 叶轮与扩压器结构参数Table 1 Structural parameters of impeller and diffuser
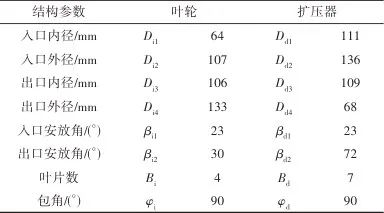
1.2 实验工况
2 实验结果与讨论
2.1 单相水力性能

![]() | (1) |




![]() | (2) |
![]() | (3) |


2.2 气液两相surging test
![]() | (4) |

![]() | (5) |
![]() | (6) |
![]() | (7) |

